Plures Intelligens Modicum Machinatorem
808 Gilman Street Berkeley, CA 94710 | 510-549-3300 | admin@bearinc.com
Dr. Glen Stevick, P.E. ext. 101 | Dr. Dave Rondinone, P.E. ext. 102 | Derek King, P.E. ext. 103 | Mingxi Zheng, P.E. ext. 106
Fatigue and Materials Deterioration.
Fatigue is a process by which materials wear down over continued and repetitive use. Just as a human can fatigue, so can a material. The repetitive forces and cycles that a material can be subjected to may lead to failure as each cycle weakens and breaks more and more bonds. Usually, during the design phase of a product, hypothetical lifetimes are use to help determine the design and materials used to ensure the product will survive. However, if these lifetimes are not accurate, or if the wrong design or material is used, this could lead to early and catastrophic failure.
BEAR engineers can use both mathematical and physical models to characterize fatigue failure. A couple examples are shared below.
fatigue and remaining life of coke drum
Fatigue of the material is demonstrated by the crack initiation and crack growth process after the cyclic loading. Cyclic loading is a repetition of low and high stresses over a long period of time. Fatigue for a coke drum occurs primarily from the difference between the thermal strains at the heath and during the cool-down of the coking cycle. Additionally, welds are typically weaker than plate-base material in fatigue because of notches and minute flaws inside of the weld. The picture on the left shows the thermal distribution of the coke drum.
Fatigue in the skirt occurs from thermal gradients when the coke drum is hot and from differences in temperature between the skirt and shell during heat-up and cool-down. Fatigue in the shell occurs during cool-down as the cooling steam and water contact the shell in irregular patterns.
Local wrinkling of the shell and cladding disbanding are two additional problems related to high thermal stresses from the heat-up or cool-down.
crack propagating on skirt and shell weld
Using the sample of the shell weld, BEAR engineers predicted the lifetime of the material by artificially cycling thermal stresses for certain period of time.
Experimental Process:
-
Crack growth is observed at the root and toe of the skirt to shell weld.
-
During the eight initial cycles, crack growth is measured.
-
Prediction of significant cracking within 3 to 6 years is provided.
-
Recommendations to increase the lifetime of the coke drum are calculated.
measuring the shell fatigue
-
Determination of what are the important process variable on shell fatigue in specific case (environmental factors, external force).
-
Prediction of lifetime of shell with high accuracy.
-
Recommendations to increase the lifetime of the shell are calculated.
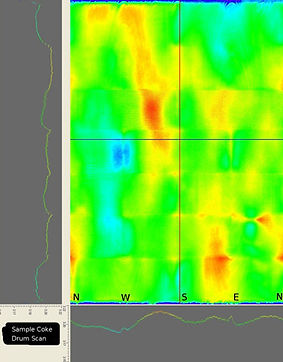
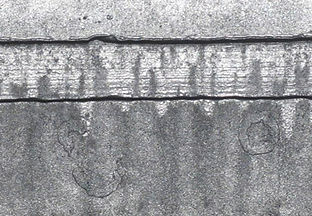